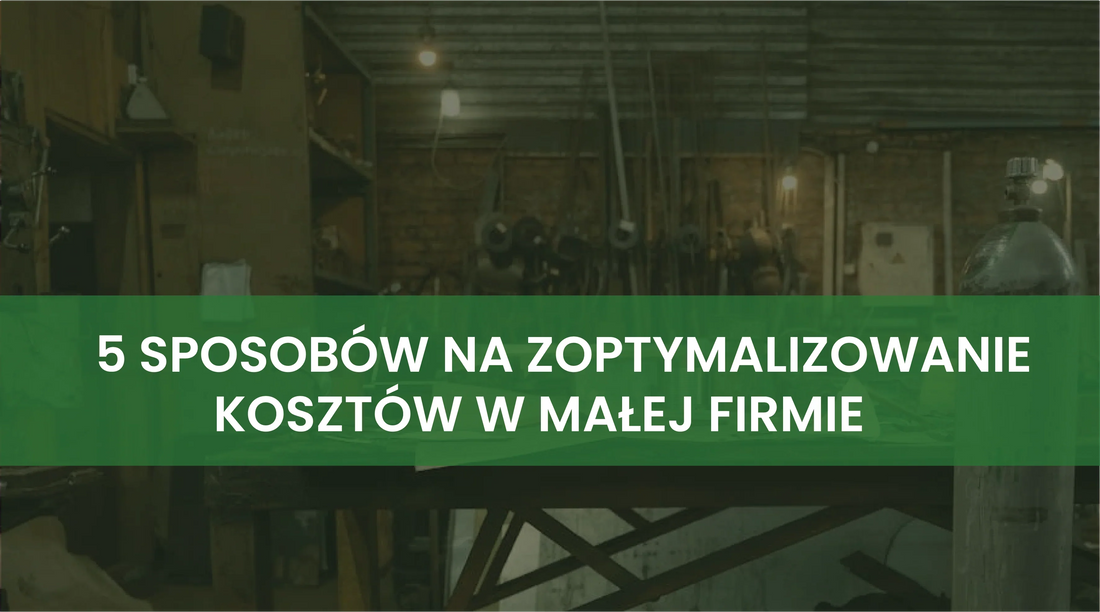
5 sposobów na zoptymalizowanie kosztów spawania w małej firmie
Koszty spawania mogą wydawać się nieuniknione, ale z odpowiednim podejściem możesz je znacząco obniżyć, nie rezygnując z jakości. Jeśli prowadzisz małą firmę, każda oszczędność się liczy. Dlatego przedstawiamy pięć konkretnych strategii, które pomogą Ci zoptymalizować wydatki na spawanie.
1. Staranny wybór materiałów spawalniczych
Materiały spawalnicze to jeden z największych kosztów w każdej firmie. Jak możesz zaoszczędzić? Przede wszystkim wybieraj takie materiały, które odpowiadają specyficznym wymaganiom Twojej produkcji. Często droższe rozwiązania mają zamienniki o podobnych właściwościach mechanicznych i chemicznych.
Pro-tip: Na początek przeprowadź dokładny audyt materiałów, których używasz. Współpracuj z dostawcami, którzy przyjrzą się twojej produkcji, i wybiorą materiały spawalnicze które są najlepiej dopasowane do twoich potrzeb.
2. Optymalizacja procesów pracy
Niewłaściwe planowanie to cichy zabójca rentowności. Każda minuta przestoju lub nieprzemyślana sekwencja zadań może generować straty. Dlatego wprowadź harmonogramy, które uwzględniają dostępność sprzętu, ludzi i materiałów.
Skorzystaj z prostych narzędzi do planowania, takich jak arkusze kalkulacyjne, lub bardziej zaawansowanych systemów ERP, które integrują wszystkie aspekty produkcji. Dobrze przemyślane procesy pozwalają także lepiej kontrolować zużycie materiałów – dokładne wyliczenie ilości potrzebnych elektrod czy gazów technicznych może wyeliminować problem nadprodukcji.
3. Regularna konserwacja sprzętu
Zaniedbany sprzęt to prosta droga do większych kosztów. Niesprawne urządzenie nie tylko obniża jakość spawów, ale może prowadzić do awarii i kosztownych przestojów. Regularna konserwacja i wymiana zużytych części są kluczowe.
Co możesz zrobić? Sporządź harmonogram serwisowy, uwzględniając zalecenia producenta. Warto również przeszkolić swoich pracowników, aby potrafili diagnozować podstawowe problemy i samodzielnie przeprowadzać drobne naprawy.
Dobrze jest również inwestować w części zamienne. Posiadanie ich na stanie pozwala zaoszczędzić czas i pieniądze, gdy sprzęt wymaga natychmiastowej naprawy.
4. Optymalizacja zużycia gazów osłonowych
Gazy osłonowe, takie jak argon, dwutlenek węgla czy mieszanki, są nieodłącznym elementem wielu procesów spawania. Ich koszty mogą jednak szybko narastać, jeśli nie zostaną odpowiednio zarządzane. Jak to zrobić?
Pierwszym krokiem jest kontrola przepływu gazu. Zbyt wysoki przepływ może prowadzić do strat i marnotrawienia zasobów, natomiast zbyt niski powoduje problemy z jakością spoin. Inwestycja w precyzyjne regulatory i mierniki to prosty sposób na zmniejszenie zużycia gazu.
Warto także analizować, które mieszanki gazowe są naprawdę potrzebne. Często tańszy dwutlenek węgla może zastąpić droższy argon w określonych zastosowaniach bez utraty jakości.
5. Monitorowanie i analiza kosztów produkcji
„Co nie jest mierzone, nie może być poprawione” – to zasada, która doskonale sprawdza się w optymalizacji kosztów spawania. Regularne monitorowanie wydatków pozwala zidentyfikować obszary, w których można wprowadzić zmiany.
Zacznij od śledzenia kosztów materiałów, energii, pracy i konserwacji sprzętu. Wprowadź prosty system raportowania, w którym pracownicy będą notować zużycie materiałów i czas pracy na poszczególnych zadaniach.
Następnie analizuj dane. Na przykład, jeśli zauważysz, że zużycie elektrod jest wyjątkowo wysokie w konkretnym procesie, możesz rozważyć zmianę techniki spawania lub przeszkolenie pracowników. W przypadku energii przydatne mogą być liczniki zużycia prądu zainstalowane bezpośrednio na urządzeniach.
Tego rodzaju podejście nie tylko pozwala na oszczędności, ale również zwiększa przejrzystość procesów w firmie.
Podsumowanie
Optymalizacja kosztów spawania w małej firmie to proces, który wymaga przemyślanych działań, ale przynosi realne oszczędności i podnosi efektywność pracy. Kluczem jest podejście wielowymiarowe – od wyboru odpowiednich materiałów, przez inwestycję w nowoczesny sprzęt i szkolenia pracowników, aż po automatyzację i regularną konserwację urządzeń.
Nie zapominaj także o monitorowaniu kosztów i wprowadzaniu zmian na podstawie analizy danych. Często nawet drobne poprawki, takie jak kontrola przepływu gazów osłonowych czy lepsze planowanie harmonogramu pracy, mogą przynieść zaskakująco duże oszczędności.
Pamiętaj, że każda inwestycja w optymalizację to nie tylko mniejsze wydatki, ale także większa konkurencyjność Twojej firmy na rynku. Zacznij od jednego obszaru, wprowadź zmiany i obserwuj rezultaty. Sukces w optymalizacji kosztów to kwestia systematycznego podejścia i konsekwencji. Każdy krok w kierunku lepszej efektywności to krok w stronę sukcesu Twojej firmy!
Jeśli zainteresował Cię temat ten temat, koniecznie sprawdź inne nasze artykuły i poradniki z Porady spawalnicze
Masz pytania? Skontaktuj się z nami – nasi eksperci chętnie pomogą w rozwiązaniu Twoich wątpliwości i doradzą w wyborze najlepszych materiałów.
A gdy będziesz gotowy, zapraszamy do zapoznania się z naszą ofertą. Wysokiej jakości produkty czekają na Ciebie – sprawdź teraz!